VAS
VAS:
- Ticketing
- Sorting including Shade Sorting
- Return Processing Inspection and Rework
- Repackaging
- Quality Inspection
- Gift Set Assembly
- Sorting and Resizing
- Garment Label Redline/Blackout
- Barcoding
- Hang Tags/Joker Tags
- Bagging
- Measurement
- Counting
- Glue Dot Application and Water Seal Application
- VELCRO Application
- Collation
- Cello/Shrink/Bundle/Band
- Heat Seal Machinery
- Laundry Services
- Bulk to Pre-Pack or Pre-Pack to Bulk
- Returns Rework and Refurbishing
- Batch Code Printing and Labeling
A streamlined process that fits your project and deadline

Sort and Pack is committed to consistent response and high quality Value Added Services (VAS). The VAS services that we provide cover a wide variety of customers’ needs serving many industries — including print, retail, wholesale, medical supplies, promotional, manufacturing, advertising, etc.
We focus on solutions that are timely, flexible, cost-effective and quality conscious, to meet your demands. Attention given to brand integrity and high quality production standards, while meeting time-sensitive deadlines, are the hallmarks of our success.
Flexibility and adaptability are critical to fulfill your needs and objectives. We adjust our facility and work stations to meet the project needs — from traditional services to highly complex performance standards, including short- and long-term projects from small batch to high volume production. We often work on tight timelines and will add extra shifts and/or weekends and holidays to meet your needs.
High quality packaging
Safe Packaging to Eliminate Damage
Sort and Pack offers special packaging services for products that require extra protection. For fragile or breakable items, we individually wrap products in bubble wrap before packaging the product for shipping, including:
- Shrink, bundle-wrapping, blister pack, gift pack, displays
- Multi-packs, tray packs, banding
- Clamshell, flow-wrap, fin-seal, thermoform
- Counter, floor, end-cap and clip-strip displays
- Cello wrapping (cosmetics, gift wraps)
For example, liquid dietary supplements are bottled in special MIRON violet glass to block out full spectrum light and to avoid the degrading effect that light could have on the product. For products that could potentially break and leak:
- We wrap each bottle individually in expandable, absorbent paper
- We affix product-identifying stickers so it can be easily recognized in inventory
- We ensconce the product in bubble wrap prior to shipping
- We can also include product and packaging inserts, such as directions and instructions, product return information and more
Secure shipments ensure quality and accuracy
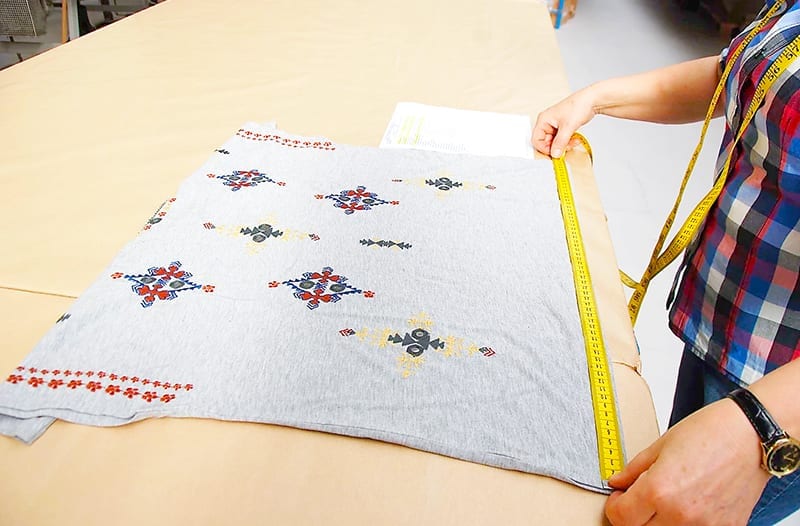
Completed kits are stored with your inventory and mapped to a specific SKU distinct from those assigned to products that may be shipped separately. The shipment SKUs are mapped to facilitate inventory as well as shipment tracking.
Sort and Pack’s team can prepare volumes of pre-packaged kits to have ready for your future order shipments and our account managers can map new kit SKUs anytime you need to add them. Most shipments include some type of insert, whether an instructional manual, receipt or package return information.
In addition to knowing where all their products and materials are, our clients never have to worry about whether Sort and Pack can handle their next project. Whether 1,000 units or 1 million, Sort and Pack has a trained staff to handle the product assembly, kitting and shipping needs of our clients, after all your business is our business.
Quality Control Measures
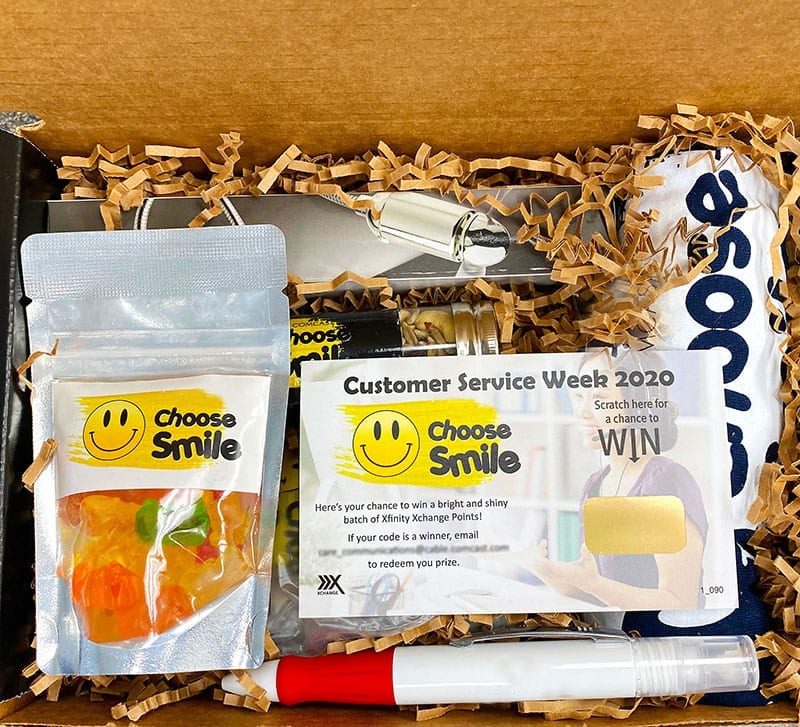
Sort and Pack’s well-defined kitting and assembly process ensures efficiency and order accuracy. Final kits are spot-checked to ensure quality as a final measure of precision.
Maintaining inventoried pre-packaged kits allow Sort and Pack’s customers to react quickly in cases of sudden increases in retail order demand. Additionally, Sort and Pack’s order-grouping technology recognizes orders shipping to an identical address and groups the products into one shipment to save our customers on both packaging and postage costs.
Quality Control Case Studies:
Product correction with assembly with pick and pack of 80,000 units of pendant necklaces
- Cut off inferior bail from pendant
- Affix new bail and pinch closed
- Open clasp of chain
- Place on a display card
- Affix price and security tickets to the display card
- Insert card into clam shell jewelry box
- Insert box into protective sleeve
- Affix price ticket
- Pick and pack by style, by store
- Ship to regional fulfillment centers
Shade inspection of 50,000 garments
- Receive goods in printer fold quantities
- Inspect garment or color shading to customer shading tolerance
- Separate unacceptable vs. acceptable
- Acceptable garments — fold, ticket, insert into poly bag, pick to prepack specifications, pack by store, apply store label, ship to fulfillment center
- Unacceptable garments — count, bulk pack, ship to fulfillment center
Storage and order case pick of 10 truckloads of packaged candy
- Receive by trailer candy with expiration date sensitive multi SKUs; solid and mixed product pallets
- Store by SKU on pallets of a standard quantity
- Pick by case order
- Label pallets per instructions for LTL shipments to stores
- Cycle count by request
Process mark out-of-stock and/or seasonal recalls for major retail chain of over 250 SKUs
- Receive multi-SKU merchandise from individual stores or regional return centers
- Verify merchandise against manifest or packing list
- Maintain inventory of items received by SKU
- Inspect all merchandise
- Repair/re-sew labels as needed
- Fold
- Replace packaging if needed
- Re-ticket as necessary
- Store inventory
After customer evaluates inventory:
Option 1:
Replace price tickets
Pick/Pack by store
Ship to fulfillment center or re-label and ship direct stores
Option2:
Remove price tickets
Prepare shipment for sell-off
- Inspection and re-work of customer returns processing
- Receive gaylords of returned mixed merchandise
- Remove merchandise from bag
- Inspect for any default
- Use lint roller and dry sponge as needed to remove any foreign particles from garment
- Re-bag acceptable merchandise in new size appropriate poly bag
- Consolidate and bag unacceptable merchandise
Quality sort of NFL team themed winter styled jackets
- Receive floor-loaded overseas containers
- Sort and palletize cartons solid packed by team and size
- Complete 14-point quality inspection
- Re-polybag acceptable merchandise
- Provide customer summary of acceptable merchandise – Team to size
- Customer provides distribution
Pick by team and size, by PO, by store - Create packing lists and caron
- Arrange freight as needed
Wholesale & Liquidation
Wholesale services include:
- Purchasing
- Master Packing
- Solid Packing
- Ecommerce
- Bulk Distribution
- Labeling
- Ticketing
- Resale
- Consolidation
- Product Sourcing
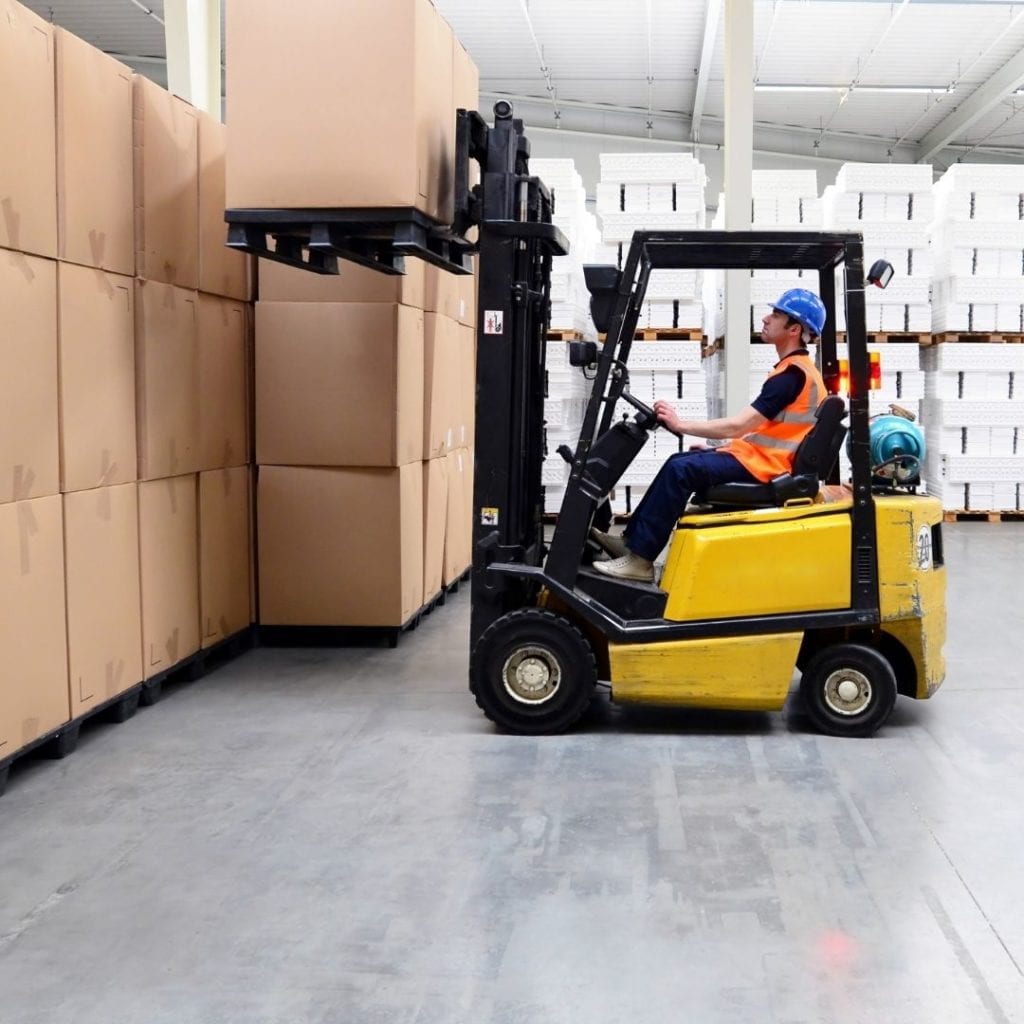
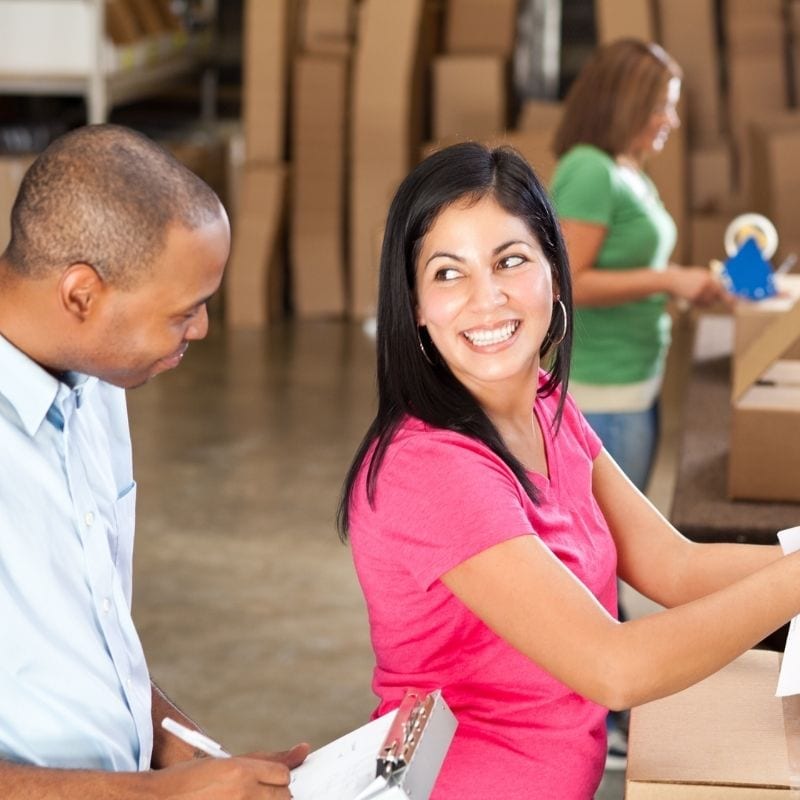
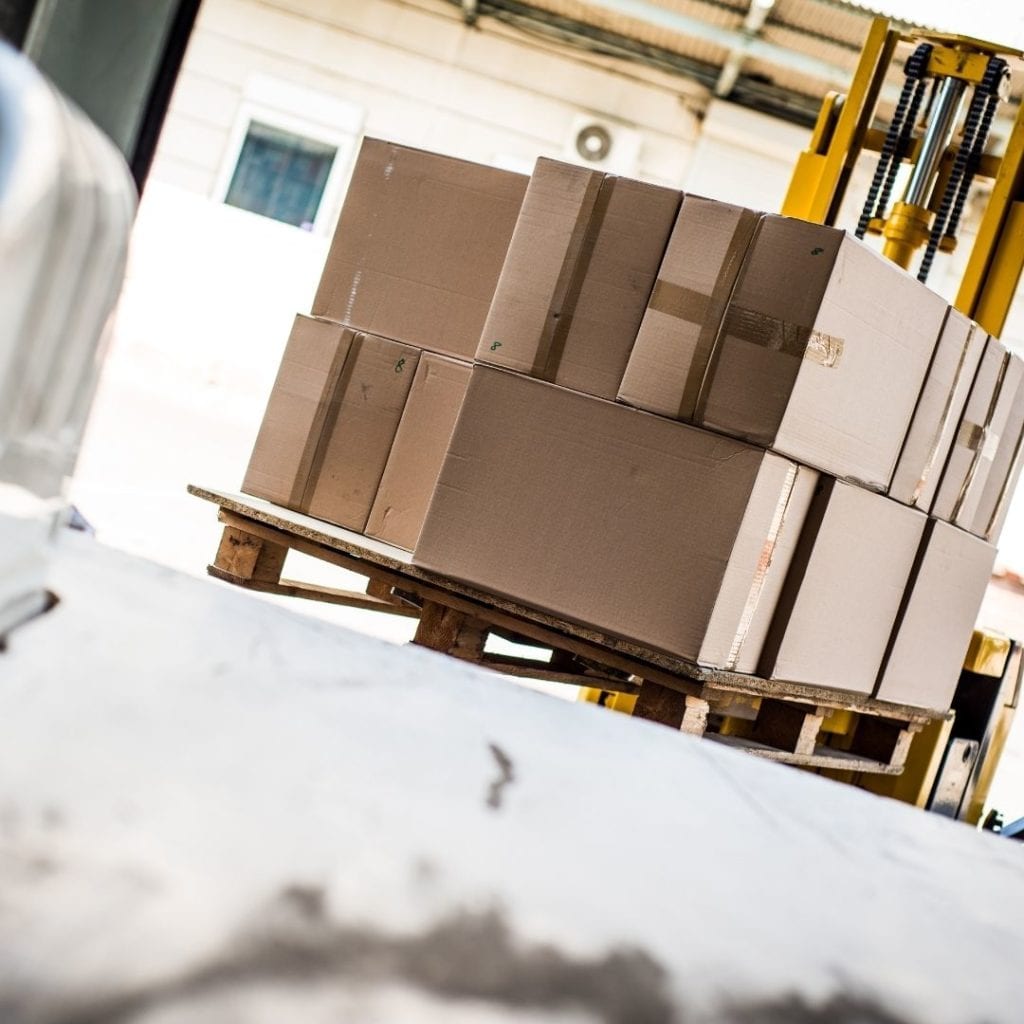
Wholesale and Liquidation Case Studies:
- Unload and storage of 40 of trailers from a hardware store liquidation
- Receive solid carton multi-SKU merchandise and store by pallet
- Verify merchandise against manifest or packing list
- Maintain inventory of items received by inbound trailer
- Re-ticket as necessary
- Pick orders by SKU
- Ship orders via truckload and LTL as directed by customer
- Unload and storage of 17 of trailers from office store liquidation
- Receive solid carton multi-SKU merchandise and store by pallet
- Verify merchandise against manifest or packing list
- Maintain inventory of items received by inbound trailer
- Re-ticket as necessary
- Pick orders by SKU
- Ship orders via truckload and LTL as directed by customer